In the world of electronic components, color ring resistors occupy an indispensable position. They mark the resistance value of the resistor in an intuitive way by painting a ring of a specific color on the surface of the resistor. This design was originally designed to simplify the identification process and help technicians quickly identify and select the resistor with the required resistance value, especially when performing circuit design or repair. Although the development of modern electronic technology has made the forms and manufacturing techniques of resistors increasingly diversified, color ring resistors still play an important role in many application scenarios, such as home appliances, electronic measuring instruments and other electronic equipment, due to their intuitiveness and convenience. Role. However, its relatively large size limits its application in highly integrated circuits to a certain extent.
In the world of resistors, there are several main types of resistors based on the material they are made of. First, carbon film resistors decompose gaseous hydrocarbons under high temperature and vacuum conditions to deposit carbon on a porcelain rod or tube, thereby forming a crystallized carbon film. By changing the thickness of the carbon film or adjusting the length of the carbon film by notching, the requirements for different resistance values can be achieved. In addition, in order to protect the carbon film from external damage, its outer layer is usually coated with epoxy resin for sealing. Carbon film resistors are widely used in various circuits due to their low manufacturing cost.
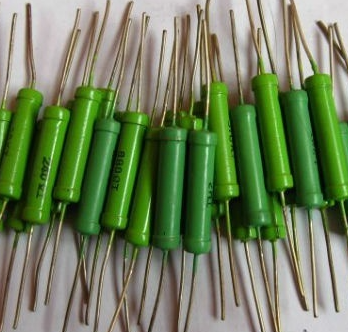
Metal film resistors take a different technical path. Heating an alloy (such as nickel-chromium alloy) in a vacuum environment causes it to evaporate and form a conductive metal film on the surface of the porcelain rod. By notching grooves or changing the thickness of the metal film, the resistance can also be precisely controlled. Compared with carbon film resistors, metal film resistors have the advantages of smaller size, higher accuracy, lower noise, and better stability, making them more popular in applications that require high accuracy and stability.
Carbon resistors are made by mixing materials such as carbon black, resin and clay, and then pressing and heat-treating them. Its resistance is also represented by a colored ring painted on the surface of the resistor. This kind of resistor is simple and durable, suitable for occasions that do not require particularly high precision.
Wirewound resistors and wirewound potentiometers represent another high-precision solution. Wirewound resistors are made by winding resistance wire (such as constantan, manganese copper or nickel-chromium alloy) around a ceramic skeleton and can be divided into fixed and variable types. They are characterized by high precision, good stability, and excellent heat resistance. They are especially suitable for occasions that require high precision and stability. Wirewound potentiometers add sliding arms and brushes on this basis to provide the function of adjustable resistance. They have the advantages of high precision, good stability, and small temperature coefficient, and are indispensable in high-performance electronic equipment. One of the components.
In general, the choice of resistor material and manufacturing process is directly related to the performance and application range of the resistor. Whether it is carbon film, metal film, carbon or wire wound, each material of resistor has its own unique characteristics and applicable scenarios. When designing electronic circuits, engineers need to carefully select the appropriate resistor type based on specific application requirements to ensure circuit performance and reliability.