DC power supply system is an indispensable part of modern electrical equipment, and its design and implementation play a vital role in ensuring the stability and reliability of power supply. This article aims to provide an in-depth look at the two core components of a DC power system - the battery screen and the DC charging screen (DC screen) - as well as their respective key functions and technical characteristics.
Battery screen configuration and functions
As the energy storage core of the DC power supply system, the battery panel is usually composed of multiple batteries, which are arranged in series to meet the needs of different voltage outputs. The size design of the battery screen (800×600×2260mm) allows it to accommodate 2V to 12V batteries ranging from 9 to 108 cells, thereby being able to provide a voltage output of 110V or 220V. When choosing a battery type, valve-regulated sealed maintenance-free lead-acid batteries are preferred due to their reliability and ease of maintenance. These batteries are designed to ensure that the DC power system can provide stable power supply under different operating conditions.
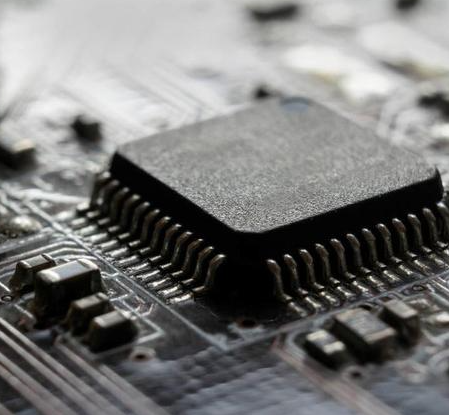
Composition and technical details of DC screen
The design of the DC panel integrates multiple key technology modules, including rectifier module system, monitoring system, insulation monitoring unit, etc. Each module assumes an indispensable function in the system. The rectifier module system is responsible for converting alternating current into direct current. Its design takes into account a variety of cooling methods and protection functions to adapt to different application needs and improve system reliability. As the brain of the system, the monitoring system ensures the efficient operation of the power system through real-time monitoring and control. The insulation monitoring unit focuses on monitoring the insulation status of the system to ensure safe operation.
Rectifier module system
The design of the rectifier module system allows multiple modules to work in parallel to achieve N+1 redundancy, thus enhancing the reliability of the system. The module can output a stable DC voltage of 110V or 220V, and has complete protection functions, such as input overvoltage protection, output overvoltage protection, current limiting protection and short circuit protection. These features ensure the stability of the power system under various circumstances. run.
surveillance system
The monitoring system obtains operating parameters and status through long-term automatic monitoring of each functional unit and battery in the system, and performs timely data processing and system control. This automated management not only improves the operating efficiency of the power system, but also simplifies operations through the human-machine interface, ensuring the continuity, reliability and safety of the system.
Insulation monitoring unit
The main task of the insulation monitoring unit is to monitor the insulation status of the DC system in real time, including the leakage resistance of the line to the ground. Once it is detected that the insulation level drops below the preset value, the system will send an alarm signal, thus ensuring the safety of the power system.